Wind Harmonics and Vibration
LIGHT STANDARD DESIGN
Light standards (pole) are designed to accommodate certain specific environmental, load and aesthetic requirements. Various standards, guidelines, and codes govern their use like the American Association of State Highway and Transportation Officials (AASHTO), American National Standards Institute (ANSI) and many local building codes. These standards and codes are based on theoretical analysis, research and current industry practice. The standards and codes take into account direct wind pressures on the pole and luminaire; bending, shear, axial and torsional stresses; secondary moment effects (the pole and fixture being off center of the pole base when the wind deflects the pole) and the effect of heat on the base material in the area adjacent to the weld. Pole design required consideration of field conditions. All variables must be taken into consideration with selecting the pole.
Poles, which perform satisfactory in many installations all over the country, may experience destruction vibration for no apparent reason at a select location. Typically poles are designed or selected based on the 50-year mean wind map found in AASHTO, ANSI or local building codes. These indicate a minimum wind load of 70+ mph, but do not take into account certain wind conditions that can create damaging vibration. Vibration is a local site-specific condition, which is many times overlooked by those selecting a pole because it is difficult to accurately predict. Vibration can be caused by steady relatively low speed wind (10-30 mph), topography or the structure the pole is mounted to can also have impact. Studies indicate that the natural turbulence of the air stream at higher wind velocities, above 30 mph, inhibit vibration. Destructive vibration is not an indication of substandard material, workmanship or design of the pole.
VIBRATIONS
There are two common types of vibration observed in poles.
First mode Vibration sometimes referred to as sway, in which the maximum deflection occurs at the top of the pole, the deflection off center is not equal from side to side and it occurs at a low frequency, approximately once cycle per second (Figure 1). This from of vibration is usually not harmful to the pole or luminaire.
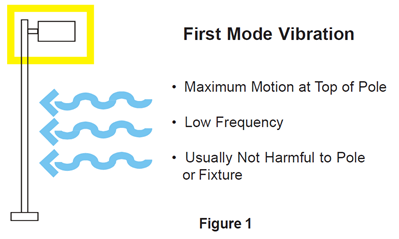
Second mode vibration can be the most damaging form of vibration and occurs approximately at the midpoint of the pole with the deflection off center equal from side to side (Figure 2). It is a higher frequency; typically three to six cycles per second.
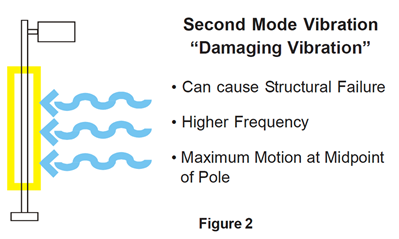
Second mode vibration occurs when the wind synchronizes with the natural pole vibration frequency. This is known as resonance (Figure 3). As the steady low level wind moves past the pole, vortices are shed alternately from either side of the structural shaft causing displacement oscillations in a direction perpendicular to that of the wind. Vortices are a swirling motion of pattern of the wind. The most serious situation arises when the vortex-shedding frequency synchronizes with the natural period of vibration in the pole, which can ultimately fatigue the pole to structural failure.
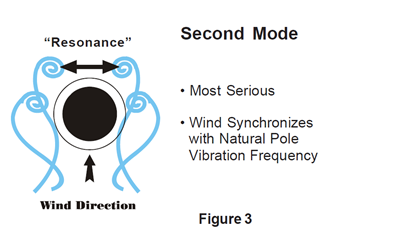
CONTRIBUTING VARIABLES
Each job site has different variable that may contribute to structural fatigue vibration. These pole variables should be taken into consideration, along with environmental and structural factors, to determine if the potential for vibration exists.
- Total Load (EPA) and Shaft Length: Light loading, less than 2.0 EPA and shaft length at or above 25 feet. These two factors when combined can be key ingredients for destructive vibration.
- Shape: Straight Square Poles have historically experienced more effects of destructive vibration over other shapes, but no shape is exempt.
- Installation Procedures: Poles are designed to carry a load. Never install a pole without the intended luminaire being installed.
ENVIRONMENTAL & STRUCTURAL FACTORS
The presence of special wind conditions in an area can be attributed to various factors. There can also be factors generated by the structure that the pole is mounted to. These factors can create the destructive conditions over an entire site or can be isolated affecting only specific pole locations on the site. If the following factors are present, be aware the conditions may exist for structural fatigue vibration to occur.
- Parking Deck Installation: Influences from surrounding structures and transferred vibration generated by moving vehicles
- Near or at airports: Little or no objects to break the wind currents and the presence of turbulence created by aircraft.
- Bridge Installation: Little or no objects to break the wind currents and the transfer of vibration generated by moving vehicles.
- Mountain Foothill Areas: Air currents traveling from the higher elevations can create steady damaging winds.
- Large Expanse of Flat Ground: In tandem with little or no structures, the wind currents will not be disrupted which sets up the possibility for low steady winds and destructive vibration.
- Steady Low Level Winds: The upper mid-west and plains states have shown this trend
Note: This is not a complete list, other factors can influence the effects of wind.
POTENTIAL SOLUTIONS
To minimize the effects of structural fatigue vibration, a device can be factory or field installed to absorb or dampen the vibration. Another option is to initially design the pole to withstand the fatigue effects if it is in an area with historical problems
The poles designed can be based on the infinite fatigue life of the materials. This option is more expensive and may not meet the budget restraints of a project, consult factory for assistance.
A more economical option is the use of factory or field installable damping devices. The field installable version is more economical than the factory installable damper and provides the flexibility of installation where and when necessary, see below.
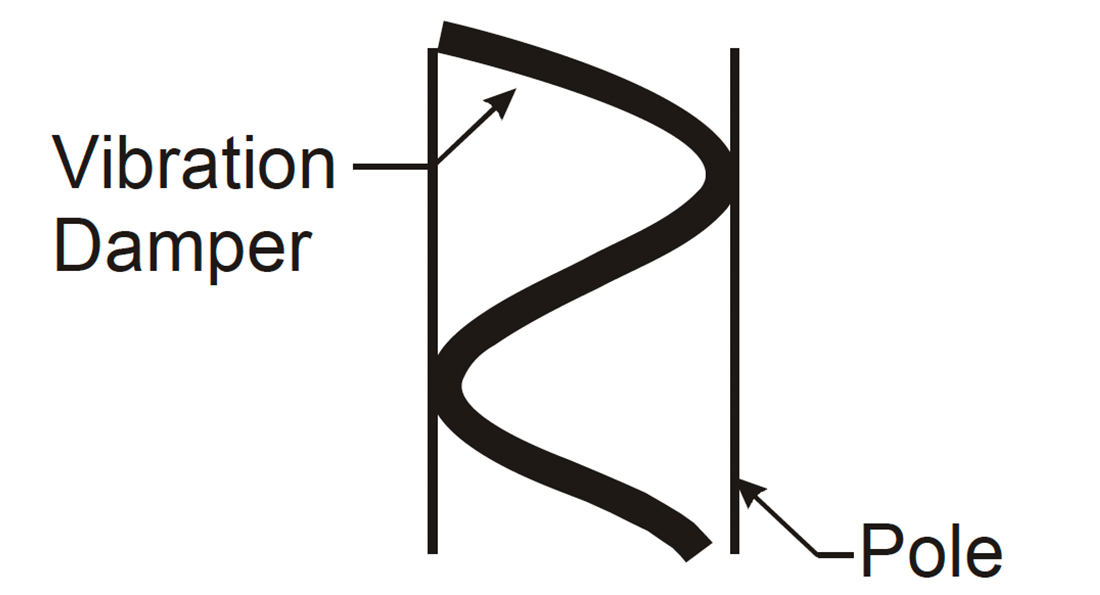
Field Installable
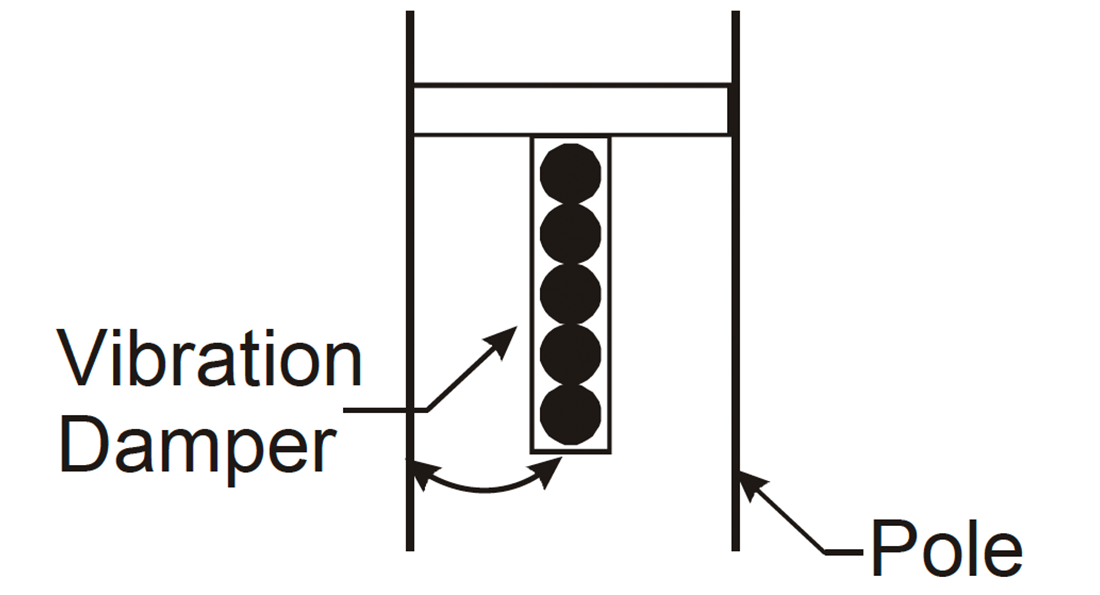
Field Installable
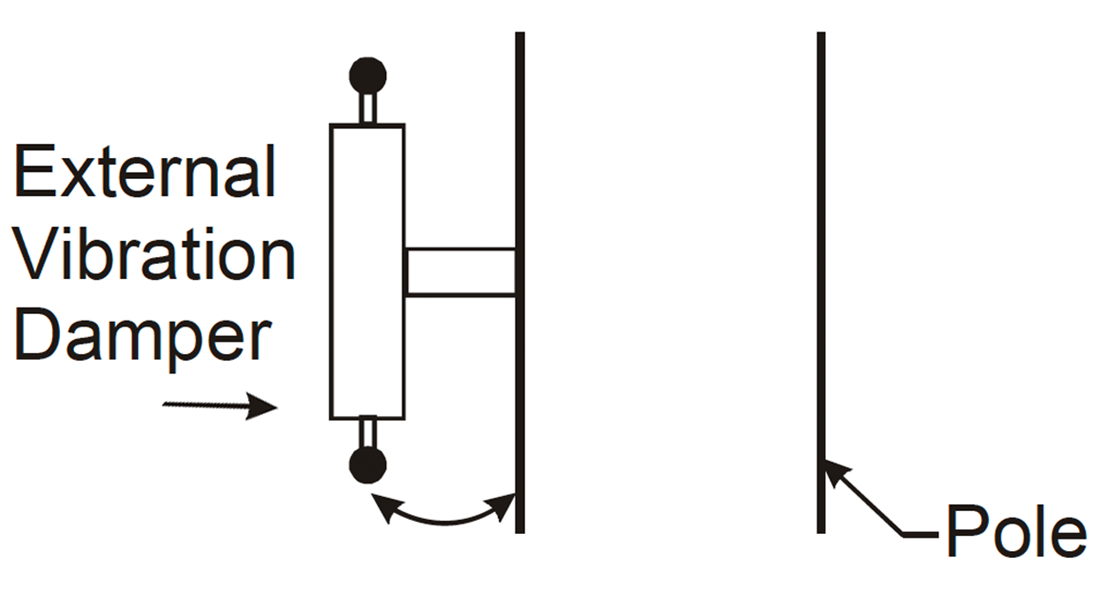
Field Installable
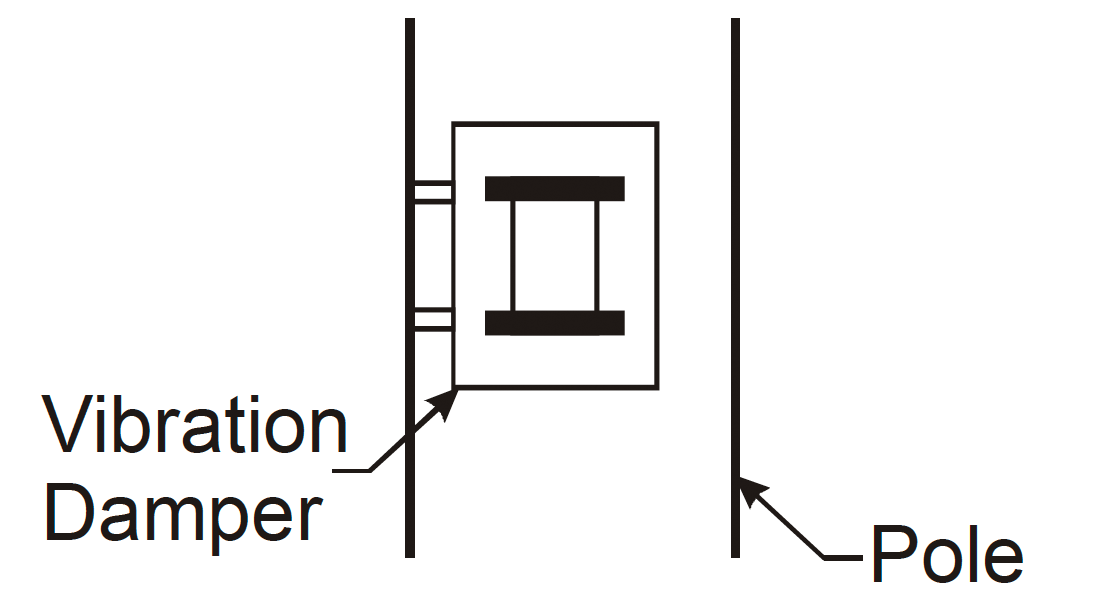
Factory Installed
Another option is the shape. Even though all pole types can experience vibration, straight square shafts seem to be more susceptible. Round tapered shafts tend to disrupt the vortex- shedding resonance state. The use of a vibration damper in conjunction with the round tapered design may be the best solution, but is not a guarantee to prevent destructive vibration.
MAINTENANCE
Poles should be included in a regular maintenance schedule like any other equipment in a facility. Every three months is a good rule of thumb. Inspecting for the effects of vibration is a very important element because if it does exist, the pole can fall in a relatively short period of time. The results can be catastrophic from luminaire failure to complete structural failure. Early signs of vibration can be visibly observed, detected by the presence of noise (humming) in the pole, loosening of attached luminaire components like sockets and lamps and short lamp life. If any of these signs exist, further inspection should be performed in the area where the shaft connects to the base plate. Look for signs of shaft material fatigue just above the entire weld in the form of hairline cracks (Figure 4).
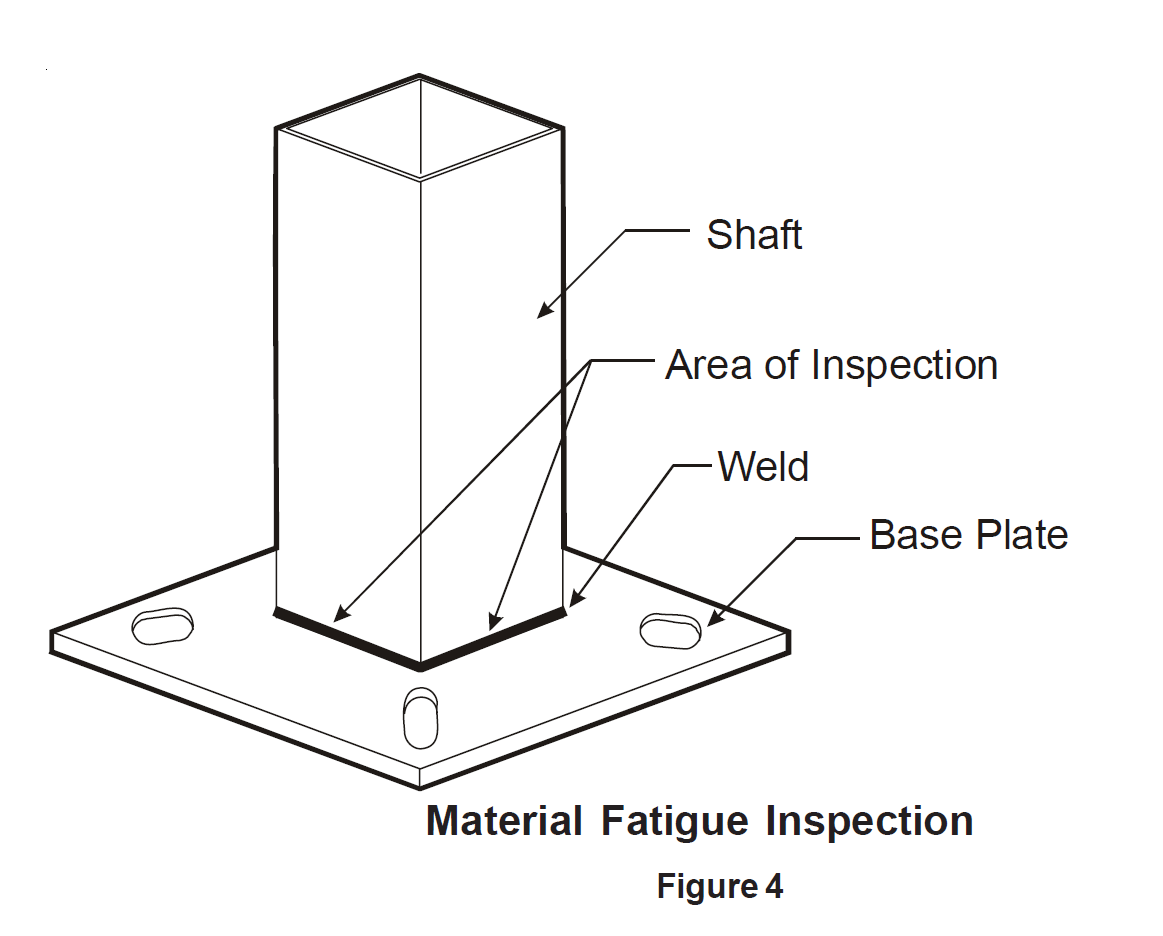
Some of the processes are:
- Visual Inspection - Typically rust will be apparent in the area of the fatigue on steel poles.
- Red die penetration test - Check for weld penetration and reveals fatigue cracks. This will work for aluminum or steel that does not show signs of rust.
- X-ray - This requires that the pole be sent to a lab which is time consuming and expensive, but necessary on occasion.
It is recommended that a licensed structural engineer be consulted to verify the problem. If material fatigue exists, the effected standards should be taken down immediately and damping devices installed in the remaining standards as soon as possible after a complete inspection. Even after the corrective measures have been performed, future inspections for the signs of vibration is a must. The information contained in this document is based on historical data and should be utilized to minimize the potential of structural fatigue occurring. Site specific variables may exist that have not been historically identified. The variables that have been identified can only approximate the potential for structural fatigue.
The information contained in this document is based on historical data and should be utilized to minimize the potential of structural fatigue occurring. Site specific variables may exist that have not been historically identified. The variables that have been identified can only approximate the potential for structural fatigue.
Wind Induced Vibrations on Light
Wind Induced Vibrations


Field Installed Vibration Damper
